Since the birth of manned air travel, the aerospace industry has been on an endless quest to make planes lighter. From Clément Ader and the Wright brothers’ first aeroplane designs to those of today, reducing weight much as possible is a determining factor. “The aerospace industry spares no expense for each kilogram saved, around 100 times more than in the automotive industry,” Patricia Krawczak, a professor at engineering school Ecole Nationale Supérieure des Mines-Télécom de Lille-Douai, says. On average, the automotive industry is prepared to pay €1 per kilogram saved, against €100–500/kg for civil aviation, and up to €10,000/kg for space travel.
Currently, composites are the most prominent materials contributing to this quest. Made from fibres (usually carbon) connected by polymer resin, composites have been increasingly used by the aerospace sector. In fact, most recent models of aircraft, like the Airbus A380 or the Boeing 787, are made from approximately half composites (along with 20% aluminium, 15% titanium and 10% steel). “We’ve reached a plateau,” Ms. Krawczak remarks, “especially since metals like titanium and aluminium are also getting better.” Composites must therefore evolve.
The promise of thermoplastics
Engineers are working towards several objectives, the first of which is to cut the costs of production. While composites do have the advantage of being lightweight and guaranteeing good mechanical performance, the cost of production is still higher than that of their metal counterparts. To make production faster and cheaper, engineers are currently looking into so-called “thermoplastic” polymers. Unlike “thermoset” polymers, which, once hardened, cannot be softened or worked, thermoplastics remain weldable, workable and even recyclable. They also do not emit volatile organic compounds, polluting gases that are often toxic.
Making composites from thermoplastics is more complicated, however, because these polymers are less fluid and permeate fibres less easily. This means that the entire production chain would have to be redesigned to make these materials fulfil the specifications of the aerospace industry. But, should it work, it would mean fewer assemblies, less waste from manufacturing, or waste that could be reused, and better recycling of parts at end-of-life.
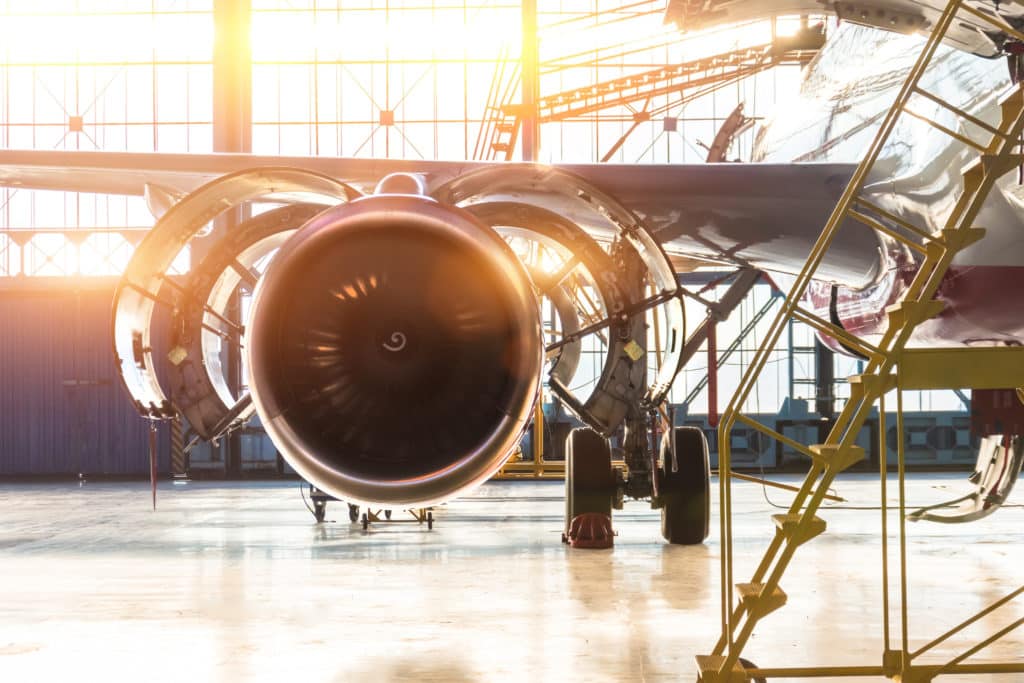
Simpler, more flexible manufacturing
Nowadays, composite parts are generally made in autoclaves, a sort of huge pressure cooker that “cures” the composite. These machines can cost as much as hundreds of thousands of Euros for the highest-performing ones, capable of producing large parts at high temperatures and under great pressure. The production cycle takes several hours, during which the equipment is locked in place. “We are working on out-of-autoclave processes, which are cheaper and more flexible, such as infusing or injecting liquid resin directly into a fibre pre-form, i.e. a ‘skeleton’ of fibrous reinforcements,” she adds. However, simplifying manufacturing processes should not impact quality. Parts must combine safety, reliability, performance – all under relatively high temperatures.
Composites also have other qualities. Notably, they are multifunctional, i.e. they provide more than just mechanical power. For example, there are self-repairing composites that integrate capsules that polymerise, and thus “heal,” the damaged part. It is also possible to insert sensors and actuators into composites that monitor the parts’ wear or reshape it on command. Other potential functions include transmitting data or producing energy through piezoelectricity to supply power to smart objects.
Additive manufacturing
Finally, thanks to additive manufacturing (3D printing), it is now possible to optimise the shape and structure of parts and components, and to design new parts. The potential gains are enormous: no more moulds or cutting, resulting in less raw material waste. “We now know how to use additive manufacturing to depose a polymer reinforced with short or continuous fibres,” Ms. Krawczak says. “This isn’t always possible, especially for larger parts, but companies such as Safran and Stelia Aerospace are working on it.” Some planes already have 3D-printed metallic parts that have passed all qualifying checks.
While it’s true that new manufacturing techniques and thermoplastics are mainly aimed at maintaining composites’ market share for the aerospace industry, design innovations could reduce the weight of parts by 20–30%, which is certainly not negligible in the context of industry efforts to decrease greenhouse gas emissions.