The so-called “disruptive” technology that is 3D printing, now in its thirties, would seem to be coming back into fashion. Yet, despite its revolutionary technical properties and advantages, as well as very optimistic growth projections, the industrial and domestic uses of this technology seem to be progressing much more slowly than expected. As such, we are still waiting for the 3D printing revolution in our day to day lives, which experts have been predicting for years. For Thierry Rayna, who has been studying the adoption and impact of additive manufacturing for years, this revolution cannot take place without combining 3D printing with other “emerging” technologies, such as artificial intelligence, connected objects and augmented reality.
What is 3D printing used for in practice?
Thierry Rayna. Broadly speaking, there are four possible uses of 3D printing 1. Firstly, rapid prototyping appeared in the 1980s and was the only possible use of this technology for a long time. Next, 3D printers started to be used to design tools (moulds, cutting guides) for traditional manufacturing methods (known as “rapid tooling”). This allows the production of moulds (for injection moulding) for example, which often have a highly complex structure, at a much lower cost and much more quickly. Production in this way allows for faster cooling and demoulding, or better performing products thanks to the possibility of printing more complex surfaces (Michelin tyres, for example).
The next step was the use of 3D printing to manufacture objects (or parts of them) directly, which offers a real cost advantage. As no tools are required for manufacturing (no moulds, etc.), the cost remains constant, and objects can be produced in very small series.
The final step is on-demand production carried out locally or even directly “at home” by consumers. This takes us from a situation in which production is based on estimated demand (hence the potential for waste), to one in which only what is needed is produced, with transportation being reserved for raw materials only. Indeed, the cost per unit in 3D printing is constant so there is much less reason to concentrate production geographically or temporally as is currently the case.
This final application is what we tend to imagine when thinking about 3D printing: domestic-use. But it should be noted that prototyping and tooling still account for ~90% of the uses of the technology. Direct manufacturing and “at home” production are (as yet) not widespread.
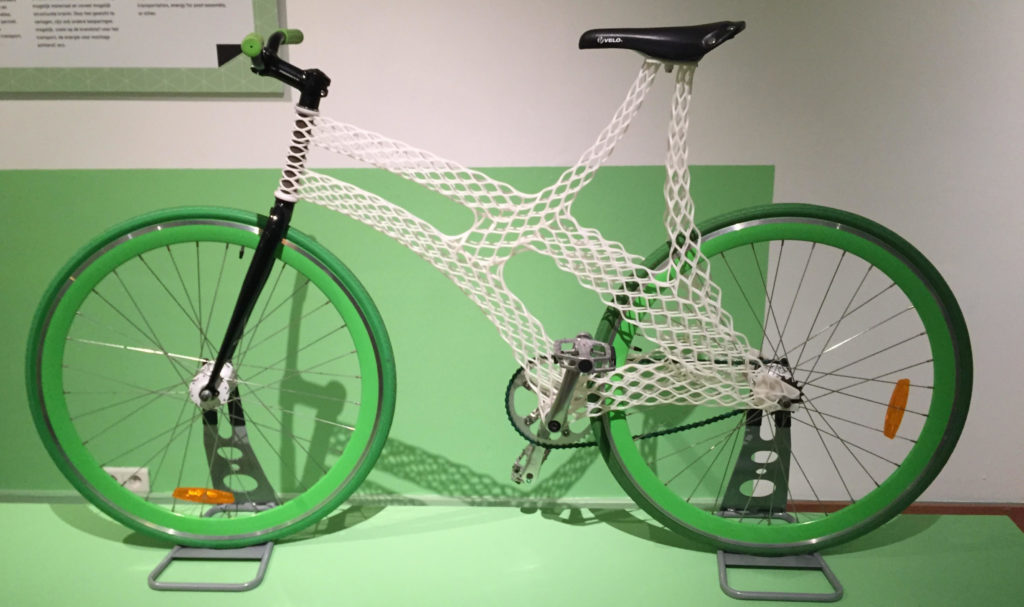
Why do you think 3D printing has not found its place in our everyday life yet?
It has in fact already been integrated into our lives for certain uses: prototyping and tooling, but these uses are not very visible and are relatively non-disruptive. For the rest, and despite the significant advantages of 3D printing, we are still looking for uses, both domestic and industrial, that really make sense.
For the moment, 3D printing is still competing with other manufacturing technologies, which are undoubtedly less “modern” but highly optimised. In fact, even though “direct manufacture” of objects (i.e., local) is the most transformative application of the technology, it is still only really justified in three very specific cases: urgency or the need for a very short lead time; the manufacture of very small series or highly personalised products; or the manufacture of objects with a very complex design. However, these needs are only critical in very specific industries such as aeronautics, medicine, space and defence. All of which are, historically, key sectors for 3D printing.
Individuals, on the other hand, might feel such needs like avoiding the need to go to the shop or waiting for a delivery, creating custom objects or printing parts for repairing domestic appliances. However, there is then a purely practical issue: using a 3D printer is currently anything but plug-and-play! You have to digitally model the object using software that is still too complex, physically calibrate the machine before each print, and hope that the printing – which can take several hours, even for the simplest object – will go smoothly.
The machines are highly sensitive, so temperature, humidity, vibrations or materials are all possible causes of failure2. If it doesn’t work properly you will have to start all over again. As for mass customisation, often perceived as the flagship argument of 3D printing, it is currently of little relevance, apart from very specific use cases like prosthetics. For a long time now, major brands have been offering the possibility of personalising objects (a pair of Nike shoes, for example), but few consumers actually do so. And customisation is nowadays limited to a few objects: what will happen when we can customise everything? Who will take the time to do it?
So, you don’t think 3D printing will take off?
Not until we find a use that really makes sense in relation to the technical (and not fantasy) characteristics of 3D printing. In direct or local manufacturing, the technology is currently only suitable for very specific sectors and under specific conditions. Rare are the cases where lead time, small series size, or the need for complexity are important. In the majority of cases, this argument does not apply for private individuals – delivery in urban areas sometimes takes less time than it takes to print the object! Moreover, even in industry, the generalisation of manufacturing using 3D printing is not a given.3
The fact that the manufacturing cost per unit remains constant is both good and bad news: as soon as the number of units produced is (relatively) high, the lack of economies of scale becomes particularly limiting. In this case, it is always more profitable to use traditional production methods. Moulds and tools are made which are certainly expensive, but they make it possible to produce tens or even hundreds of thousands of units quickly at very low unit cost.
Additive manufacturing is not a new technology, its founding patents were filed in the mid-1980s, only ten years after the creation of the first personal computers. But ten years ago, personal computers were already ubiquitous. Ten years later, widespread, accessible 3D printing remains a distant dream, despite all its ‘revolutionary’ advantages. This shows that it is not the technology that makes the ‘disruption’, but the use that is made of it. PC sales, for example, plummeted in the 1980s because people didn’t know what to do with them… then (paper) printers, digital cameras and especially the Internet came along in the 1990s, and everyone cottoned on to their appeal.
I think that 3D printing will have the same fate. Once coupled with data collection via connected objects, and subsequent processing by artificial intelligence, its usefulness will become apparent, and will thus cease to be a niche technology. It will then be possible to print a large number of objects (or more particularly relevant parts of objects), for which customisation will be fine-tuned and automatic, with real added value. But even in this case, it may be enough to have a printer in a shop nearby. It is probably more science fiction that everyone will have a 3D printer at home one day! After all, decades after their invention, not everyone has a bread maker or a yoghurt maker at home…
Interview by Juliette Parmentier